技術(shù)中心
- 汽車水室所用的PA尼龍材料解析
- 從性能方面分析尼龍6與尼龍66
- PA尼龍6纖維加相容劑的性能變化
- PA尼龍塑料改性技術(shù)劃分
- 尼龍隔熱條與PVC材料的區(qū)別
- PA尼龍原料加玻纖后的優(yōu)缺點(diǎn)概況
- 服裝上隨處可見的PA尼龍料
- PA612,PA610尼龍顆粒屬典型塑料產(chǎn)品
- 使用尼龍610,尼龍612加纖材料
- PA尼龍等原料的多種分類方法
- PA610,PA612塑料具有哪些成型性能?
- 尼龍齒輪與普通的塑料產(chǎn)品相比具有哪些優(yōu)勢?
- 聚酰胺尼龍原料在在發(fā)動機(jī)周邊的具體應(yīng)用
- PA610,PA612,PA1010物性與性能介紹
- PA612原料產(chǎn)生加工焦斑的解決方法
新聞中心
- 生物塑料或取代傳統(tǒng)塑料 指導(dǎo)行業(yè)發(fā)展方向
- 自給率低 工程塑料依賴國外進(jìn)口
- 環(huán)保出行-玻纖增強(qiáng)尼龍用于電動車
- PA尼龍原料耐磨的原因有哪些?
- 工程塑料行業(yè)未來可期!
- PA610,PA612樹脂的配色步驟
- PA尼龍原料的制造過程原來是這樣的
- 透明尼龍PA12屬于常見的3D打印材料
- PA612尼龍原料用作刷絲性能是較為不錯的!
- 透明尼龍的透明度尤為重要呢!
- 3D打印原位聚合PA6風(fēng)格獨(dú)特
- 透明尼龍需求日益旺盛,行業(yè)產(chǎn)量增高
- 日本東邦特耐克絲推出新型纖維
- 透明尼龍應(yīng)用領(lǐng)域擴(kuò)展 2022年后生物基透明尼龍市場發(fā)展空間大
技術(shù)中心>>
怎樣完善PA尼龍注塑方面的問題
怎樣完善PA尼龍注塑方面的問題:
1.注塑壓力
注塑壓力是由注塑系統(tǒng)的液壓系統(tǒng)提供的。影響熔體填充壓力的因素很多,概括起來有3類:
(1)材料因素,如塑料的類型、粘度等;
(2)結(jié)構(gòu)性因素,如澆注系統(tǒng)的類型、數(shù)目和位置,模具的型腔形狀以及制品的厚度等;
(3)成型的工藝要素。
2.注塑時間
注塑時間是指塑料熔體充滿型腔所需要的時間,不包括模具開、合等輔助時間。注塑時間要遠(yuǎn)遠(yuǎn)低于冷卻時間,大約為冷卻時間的1/10~1/15,這個規(guī)律可以作為預(yù)測塑件全部成型時間的依據(jù)。
3.注塑溫度
注塑溫度是影響注塑壓力的重要因素。注塑機(jī)料筒有5~6個加熱段,每種原料都有其合適的加工溫度(詳細(xì)的加工溫度可以參閱材料供應(yīng)商提供的數(shù)據(jù))。注塑溫度必須控制在一定的范圍內(nèi)。溫度太低,熔料塑化不良,影響成型件的質(zhì)量,增加工藝難度;溫度太高,原料容易分解。
操作過程
填充階段:填充是整個注塑循環(huán)過程中的第一步,時間從模具閉合開始注塑算起,到模具型腔填充到大約95%為止。理論上,填充時間越短,成型效率越高,但是實際中,成型時間或者注塑速度要受到很多條件的制約。
保壓階段:
保壓階段的作用是持續(xù)施加壓力,壓實熔體,增加塑料密度(增密),以補(bǔ)償塑料的收縮行為。在保壓過程中,由于模腔中已經(jīng)填滿塑料,背壓較高。在保壓壓實過程中,注塑機(jī)螺桿僅能慢慢地向前作微小移動,塑料的流動速度也較為緩慢,這時的流動稱作保壓流動。
由于在保壓階段,塑料受模壁冷卻固化加快,熔體粘度增加也很快,因此模具型腔內(nèi)的阻力很大。在保壓的后期,材料密度持續(xù)增大,塑件也逐漸成型,保壓階段要一直持續(xù)到澆口固化封口為止,此時保壓階段的模腔壓力達(dá)到最高值。
冷卻階段:
在注塑成型模具中,冷卻系統(tǒng)的設(shè)計非常重要。這是因為成型塑料制品只有冷卻固化到一定剛性,脫模后才能避免塑料制品因受到外力而產(chǎn)生變形。由于冷卻時間占整個成型周期約70%~80%,因此設(shè)計良好的冷卻系統(tǒng)可以大幅縮短成型時間,提高注塑生產(chǎn)率,降低成本。設(shè)計不當(dāng)?shù)睦鋮s系統(tǒng)會使成型時間拉長,增加成本;冷卻不均勻更會進(jìn)一步造成塑料制品的翹曲變形。
脫模階段:
注塑成型的成型周期由合模時間、充填時間、保壓時間、冷卻時間及脫模時間組成。其中以冷卻時間所占比重最大,大約為70%~80%。因此冷卻時間將直接影響塑料制品成型周期長短及產(chǎn)量大小。脫模階段塑料制品溫度應(yīng)冷卻至低于塑料制品的熱變形溫度,以防止塑料制品因殘余應(yīng)力導(dǎo)致的松弛現(xiàn)象或脫模外力所造成的翹曲及變形。
注意事項:
塑料制品設(shè)計方面。主要是塑料制品壁厚。制品厚度越大,冷卻時間越長。一般而言,冷卻時間約與塑料制品厚度的平方成正比,或是與最大流道直徑的1.6次方成正比。即塑料制品厚度加倍,冷卻時間增加4倍。
模具材料及其冷卻方式。模具材料,包括模具型芯、型腔材料以及模架材料對冷卻速度的影響很大。模具材料熱傳導(dǎo)系數(shù)越高,單位時間內(nèi)將熱量從塑料傳遞而出的效果越佳,冷卻時間也越短。
冷卻水管配置方式。冷卻水管越靠近模腔,管徑越大,數(shù)目越多,冷卻效果越佳,冷卻時間越短。冷卻液流量。冷卻水流量越大,冷卻水以熱對流方式帶走熱量的效果也越好。冷卻液的性質(zhì)。冷卻液的粘度及熱傳導(dǎo)系數(shù)也會影響到模具的熱傳導(dǎo)效果。冷卻液粘度越低,熱傳導(dǎo)系數(shù)越高,溫度越低,冷卻效果越佳。
缺陷:
注塑成型加工過程中所用的塑料原料多種多樣,模具設(shè)計的種類和形式也是五花八門,另外,操作工人對于特定注塑機(jī)的熟悉程度以及工人之間的操作技能,實踐經(jīng)驗的差異也各不相同,同時,客觀環(huán)境也會隨著季節(jié)變化而不同,這些客觀和主觀條件共同決定了注塑成型制品缺陷的產(chǎn)生。
一般來說,對于塑料制品性能優(yōu)劣的評價主要有三個方面:
第一、外觀質(zhì)量,包括完整性、顏色、光澤;
第二、尺寸和相對位置間的準(zhǔn)確性,
第三、與用途相應(yīng)的力學(xué)性能、化學(xué)性能、電學(xué)性能等。
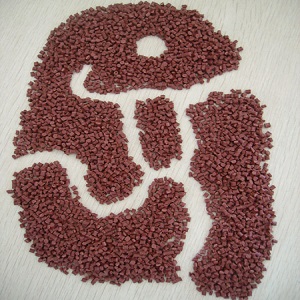
注塑壓力是由注塑系統(tǒng)的液壓系統(tǒng)提供的。影響熔體填充壓力的因素很多,概括起來有3類:
(1)材料因素,如塑料的類型、粘度等;
(2)結(jié)構(gòu)性因素,如澆注系統(tǒng)的類型、數(shù)目和位置,模具的型腔形狀以及制品的厚度等;
(3)成型的工藝要素。
2.注塑時間
注塑時間是指塑料熔體充滿型腔所需要的時間,不包括模具開、合等輔助時間。注塑時間要遠(yuǎn)遠(yuǎn)低于冷卻時間,大約為冷卻時間的1/10~1/15,這個規(guī)律可以作為預(yù)測塑件全部成型時間的依據(jù)。
3.注塑溫度
注塑溫度是影響注塑壓力的重要因素。注塑機(jī)料筒有5~6個加熱段,每種原料都有其合適的加工溫度(詳細(xì)的加工溫度可以參閱材料供應(yīng)商提供的數(shù)據(jù))。注塑溫度必須控制在一定的范圍內(nèi)。溫度太低,熔料塑化不良,影響成型件的質(zhì)量,增加工藝難度;溫度太高,原料容易分解。
操作過程
填充階段:填充是整個注塑循環(huán)過程中的第一步,時間從模具閉合開始注塑算起,到模具型腔填充到大約95%為止。理論上,填充時間越短,成型效率越高,但是實際中,成型時間或者注塑速度要受到很多條件的制約。
保壓階段:
保壓階段的作用是持續(xù)施加壓力,壓實熔體,增加塑料密度(增密),以補(bǔ)償塑料的收縮行為。在保壓過程中,由于模腔中已經(jīng)填滿塑料,背壓較高。在保壓壓實過程中,注塑機(jī)螺桿僅能慢慢地向前作微小移動,塑料的流動速度也較為緩慢,這時的流動稱作保壓流動。
由于在保壓階段,塑料受模壁冷卻固化加快,熔體粘度增加也很快,因此模具型腔內(nèi)的阻力很大。在保壓的后期,材料密度持續(xù)增大,塑件也逐漸成型,保壓階段要一直持續(xù)到澆口固化封口為止,此時保壓階段的模腔壓力達(dá)到最高值。
冷卻階段:
在注塑成型模具中,冷卻系統(tǒng)的設(shè)計非常重要。這是因為成型塑料制品只有冷卻固化到一定剛性,脫模后才能避免塑料制品因受到外力而產(chǎn)生變形。由于冷卻時間占整個成型周期約70%~80%,因此設(shè)計良好的冷卻系統(tǒng)可以大幅縮短成型時間,提高注塑生產(chǎn)率,降低成本。設(shè)計不當(dāng)?shù)睦鋮s系統(tǒng)會使成型時間拉長,增加成本;冷卻不均勻更會進(jìn)一步造成塑料制品的翹曲變形。
脫模階段:
注塑成型的成型周期由合模時間、充填時間、保壓時間、冷卻時間及脫模時間組成。其中以冷卻時間所占比重最大,大約為70%~80%。因此冷卻時間將直接影響塑料制品成型周期長短及產(chǎn)量大小。脫模階段塑料制品溫度應(yīng)冷卻至低于塑料制品的熱變形溫度,以防止塑料制品因殘余應(yīng)力導(dǎo)致的松弛現(xiàn)象或脫模外力所造成的翹曲及變形。
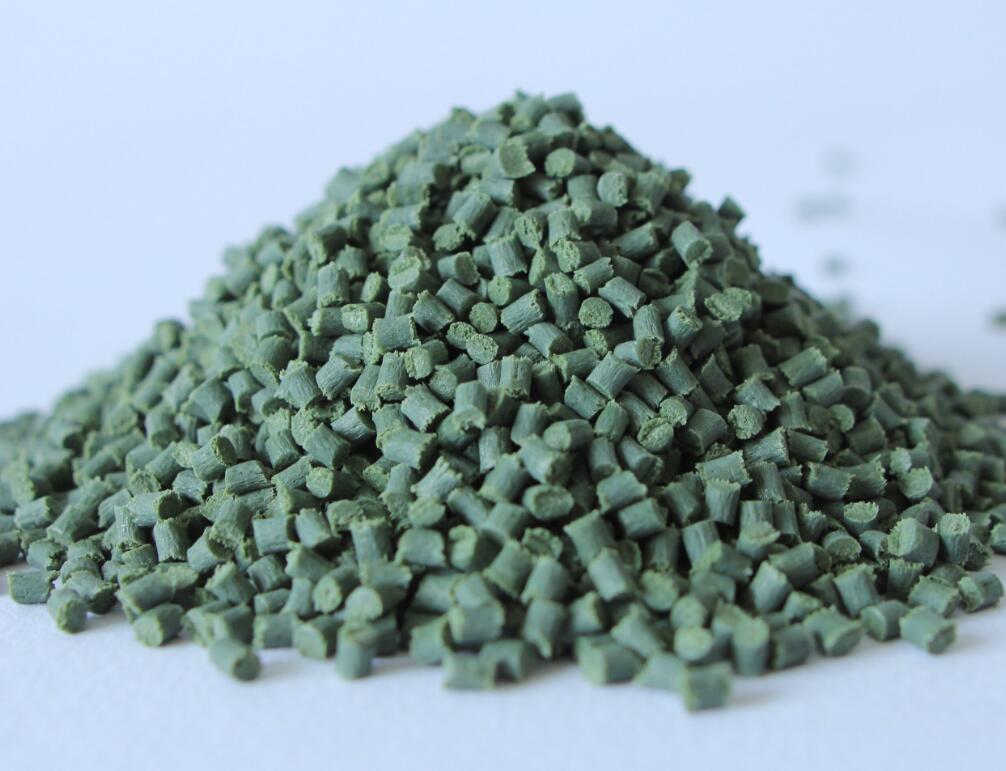
塑料制品設(shè)計方面。主要是塑料制品壁厚。制品厚度越大,冷卻時間越長。一般而言,冷卻時間約與塑料制品厚度的平方成正比,或是與最大流道直徑的1.6次方成正比。即塑料制品厚度加倍,冷卻時間增加4倍。
模具材料及其冷卻方式。模具材料,包括模具型芯、型腔材料以及模架材料對冷卻速度的影響很大。模具材料熱傳導(dǎo)系數(shù)越高,單位時間內(nèi)將熱量從塑料傳遞而出的效果越佳,冷卻時間也越短。
冷卻水管配置方式。冷卻水管越靠近模腔,管徑越大,數(shù)目越多,冷卻效果越佳,冷卻時間越短。冷卻液流量。冷卻水流量越大,冷卻水以熱對流方式帶走熱量的效果也越好。冷卻液的性質(zhì)。冷卻液的粘度及熱傳導(dǎo)系數(shù)也會影響到模具的熱傳導(dǎo)效果。冷卻液粘度越低,熱傳導(dǎo)系數(shù)越高,溫度越低,冷卻效果越佳。
缺陷:
注塑成型加工過程中所用的塑料原料多種多樣,模具設(shè)計的種類和形式也是五花八門,另外,操作工人對于特定注塑機(jī)的熟悉程度以及工人之間的操作技能,實踐經(jīng)驗的差異也各不相同,同時,客觀環(huán)境也會隨著季節(jié)變化而不同,這些客觀和主觀條件共同決定了注塑成型制品缺陷的產(chǎn)生。
一般來說,對于塑料制品性能優(yōu)劣的評價主要有三個方面:
第一、外觀質(zhì)量,包括完整性、顏色、光澤;
第二、尺寸和相對位置間的準(zhǔn)確性,
第三、與用途相應(yīng)的力學(xué)性能、化學(xué)性能、電學(xué)性能等。
如果您有關(guān)于怎樣完善PA尼龍注塑方面的問題的需求或者疑問,可以撥打電話與我們共同探討交流,歡迎您的來電!
尼龍PA610樹脂 尼龍PA612樹脂 尼龍PA1010樹脂 尼龍PA1212樹脂 技術(shù)咨詢熱線:18602297376